Various electrical facilities are in operation at the plant that "receive" power from TEPCO, "generate" power in-house, "distribute" power by adjusting the received and generated power to a specified voltage, and "transmit" power to the companies for which we are the power suppliers. To ensure a stable supply of electrical power, our Electric and Instrument Team routinely inspects all of these facilities from the viewpoint of preventive maintenance and performs maintenance to prevent failures.
Another important task is the design of modifications that will not only maintain the status quo, but also improve current power generation facilities. In my second year with the company, I was also entrusted with the task of upgrading the two highest-capacity power lines in the plant to enable more flexible operation. Thus far, the use of each of these circuits had been determined based on receiving and distributing power, which placed significant restrictions on the availability for periodic repairs and limited the measures that could be taken in the event of the occurrence of sudden issues. We were able to eliminate these operational restrictions to a great extent and modified the facility to enable flexible operation in all cases.
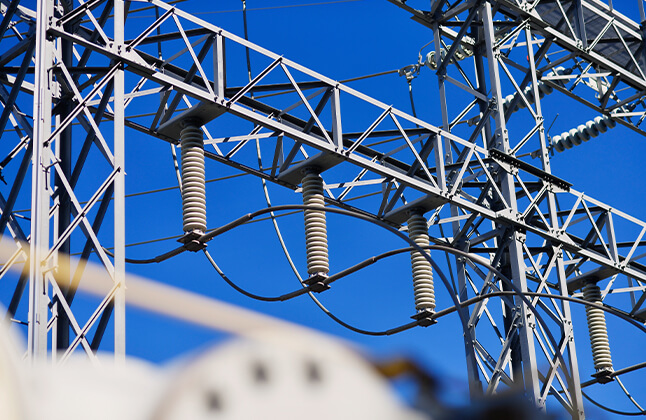
Our knowledge and technology have finally caught up with the level of the manufacturers and we are finally able to take the lead on planning.
Failure is not an option when conducting equipment retrofitting work. This was a project involving high levels of responsibility, as any errors in the design or construction might affect the entire southern power generation facility. The most important work, which accounts for the majority of the modifications, was the enhancement of the "protective coordination equipment" that disconnects the accident point within the shortest possible time in the event of an electrical accident and continues to supply power to normal circuits. I worked with the manufacturer on the design of this equipment, but in the first few months I lacked the necessary skill in reading the drawings and was unable to understand the manufacturer's proposal.
Nevertheless, as I read through the huge volume of more than 200 drawings, I gradually began to grasp the whole picture. I even reached the level where I was able to make proposals as well. As design and construction proceeded, we completed a series of unit tests with favorable results, and it was truly like a weight had been lifted from our shoulders. At the same time, I felt that I had acquired valuable experience and that my technical skills had improved significantly.