Planning the implementation of periodic refurbishment of various machinery and equipment installed in the power plant to ensure stable operation and management of construction work. The mission of the Equipment Management Group's Machinery Team is to manage the entire series of processes from the consideration of new equipment introduction, to ordering, installation, acceptance inspections and commissioning. As the limited seven-member team manages all of the facilities installed in the vast power plant, much of the work involves desk work, such as holding meetings to discuss implementation and preparing materials for such meetings, while the actual repair work itself is outsourced to a subcontractor.
The equipment I was previously in charge of was boilers, but now I am mainly looking at power generation turbines that are turned using steam generated by the boilers. This is a large rotating machine that is approximately 15 m long and 4 m wide with a high output of 70,000 kW. Temperature and vibration are constantly monitored during operation, and changes in these figures are used to predict wear and deterioration, and this in turn is connected to the planning of periodic refurbishment plans.
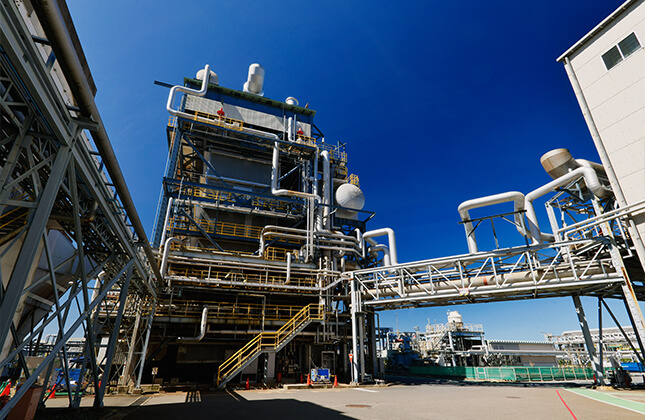
I was given the responsibility of installing new equipment and was able to install a system that achieved stable operation.
Between 2018 and 2020, a project was undertaken to install a gas turbine power generation facility that would have a lower environmental impact. I participated in this project as a mechanical engineer and was entrusted with a major role in construction supervision, from the equipment review stage before construction began, to foundation work, installation, piping, painting, and trial operation. This is the next generation of our company's main power generation equipment, and I felt a great deal of responsibility and pressure in this role. I visited the headquarters and regional factories of equipment and piping manufacturers to check on the progress, and at one point I even traveled to a factory in Korea once a month to check on the status of boiler production.
Because of this deep commitment to the project, it was a truly moving experience to see the turbine turn during trial operation. But that was only a new starting point. Operation continued to be unstable for a while, and I had to perform a lot of troubleshooting. Now it has finally reached a state where it is operating in a stable manner, and it is the mainstay of the South Kashima Power Plant.